Керамика
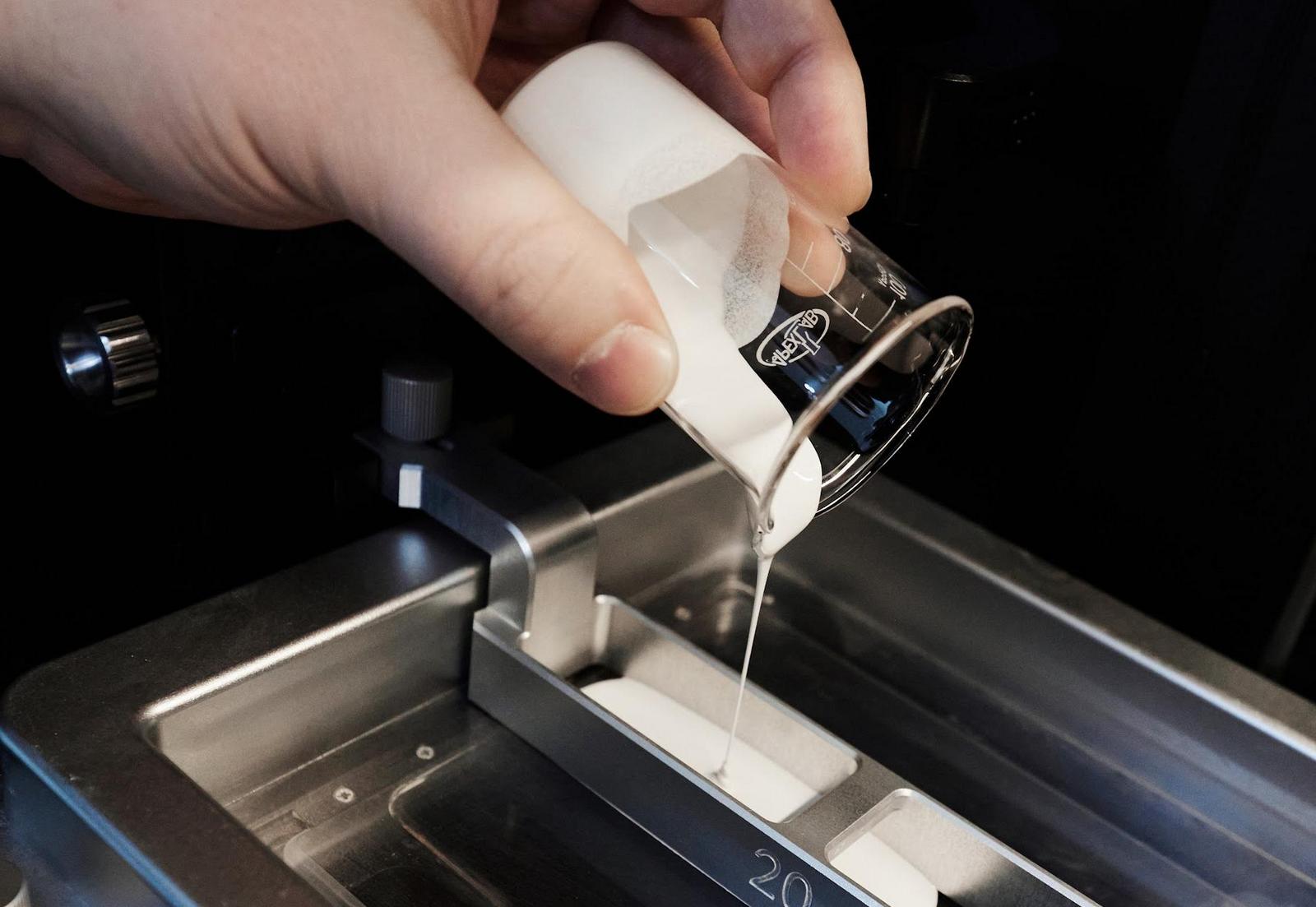
Высокоточная печать керамикой и металлами
Процесс формообразования изделий сложной геометрии из керамики предполагает либо аддитивное выращивание (DLP-процесс, штучное, мелко- и среднесерийное производство), либо инжекцию шликера в пресс-формы (MIM/CIM технологии, крупносерийное производство). 3D-печать использует вариант связующего на основе фотополимерной смолы, что в комплексе с DLP-проектором высокого разрешения дает возможности формообразования практически любой требуемой геометрии не столько с ювелирной, сколько с прецизионной точностью. Сравнение MIM/CIM технологий с DLP-процессом выглядит, как сравнение термопластавтомата и 3D-принтера – разные задачи, серии и различная стоимость подготовки производства.
Основные преимущества 3D печати известны:
- можно быстро и относительно недорого изготовить детали с геометрией высокой сложности;
- оснастка для производства не требуется;
-
полностью цифровое проектирование геометрии и возможность вносить корректировки в геометрию конечных изделий в минимальные сроки.
Сам процесс 3D печати вязкими суспензиями, содержащими керамику или металлы, похож на ставшую уже повседневной фотополимерную технологию DLP/LCD. Специальный ракель выравнивает суспензию в рабочей зоне после засветки каждого слоя.
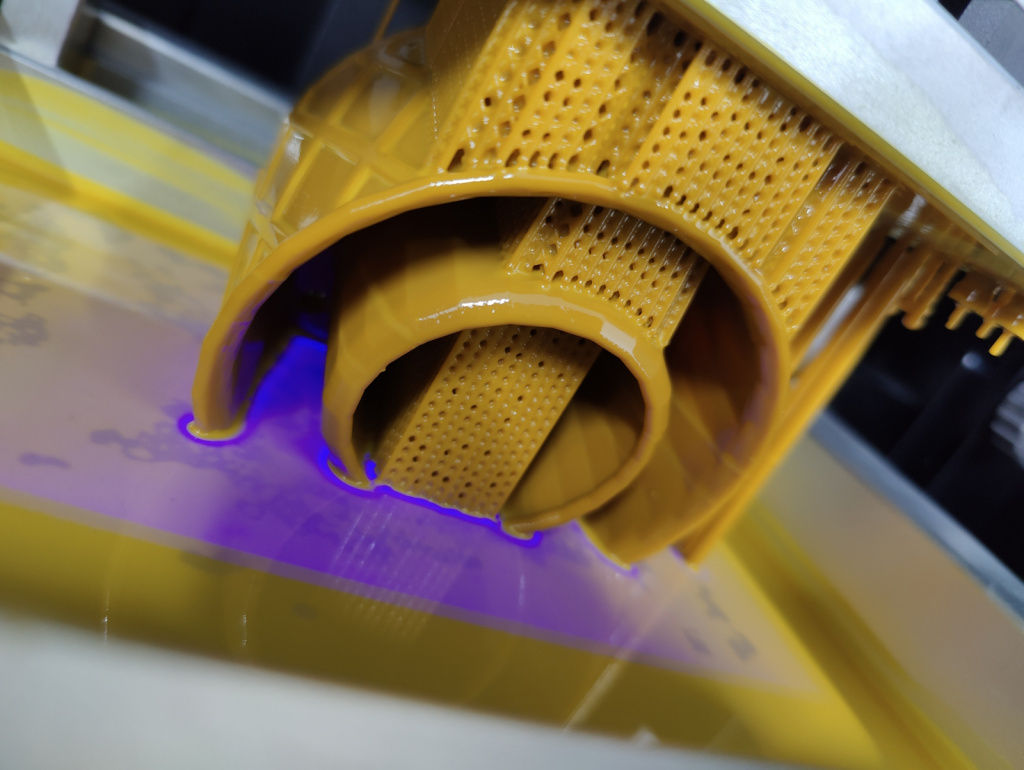
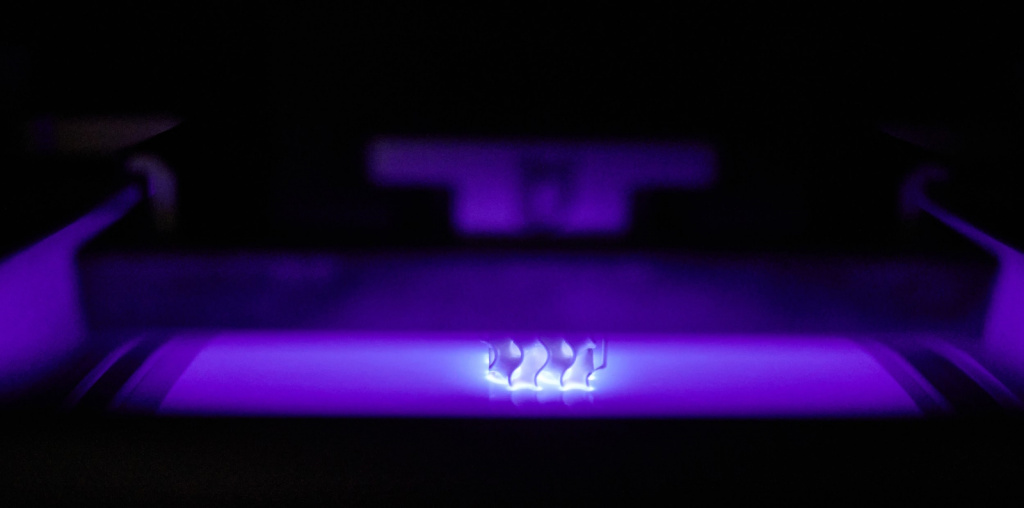
Лабораторная аддитивная установка для печати керамикой может печатать объекты величиной 96х54х100 мм с пикселем 50 мкм. Установка для мелкосерийного производства может печатать объекты размером 136х76х200 мм с пикселем 35 мкм. Установка для среднесерийного производства имеет область печати 600х600х300 мм, размер пикселя — 21,5 мкм.
Доступные для применения материалы
В качестве расходных материалов для DLP-процесса используется суспензия, состоящая из специальной фотополимерной смолы и порошка-наполнителя. В качестве наполнителя может использоваться множество функциональных конструкционных материалов. Это низкотемпературная керамика LTCC; высокотемпературная керамика Al2O3, ZrO2, SiO2; сверхвысокотемпературная керамика AlN, Si3N4, SiC; медицинская керамика TCP, HA, Bioglass; чистые металлы и сплавы: стали 316L и 17-4 PH, Inconel, Cu, Mo. Также в качестве наполнителя могут выступать всевозможные металлопорошковые композиции.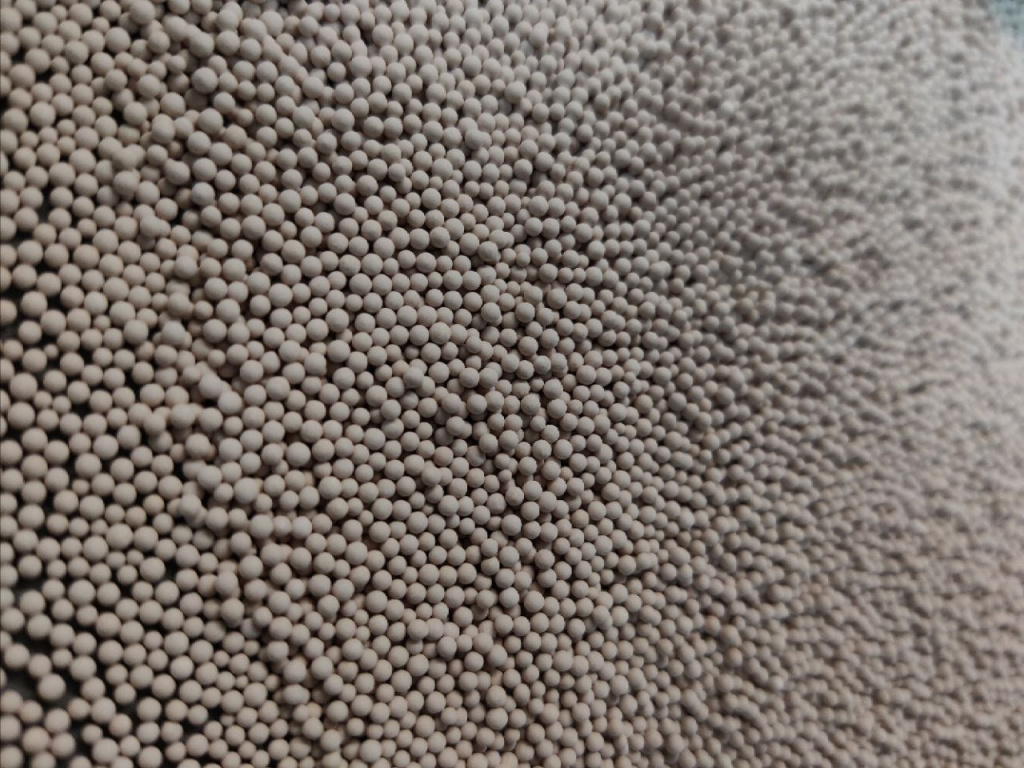
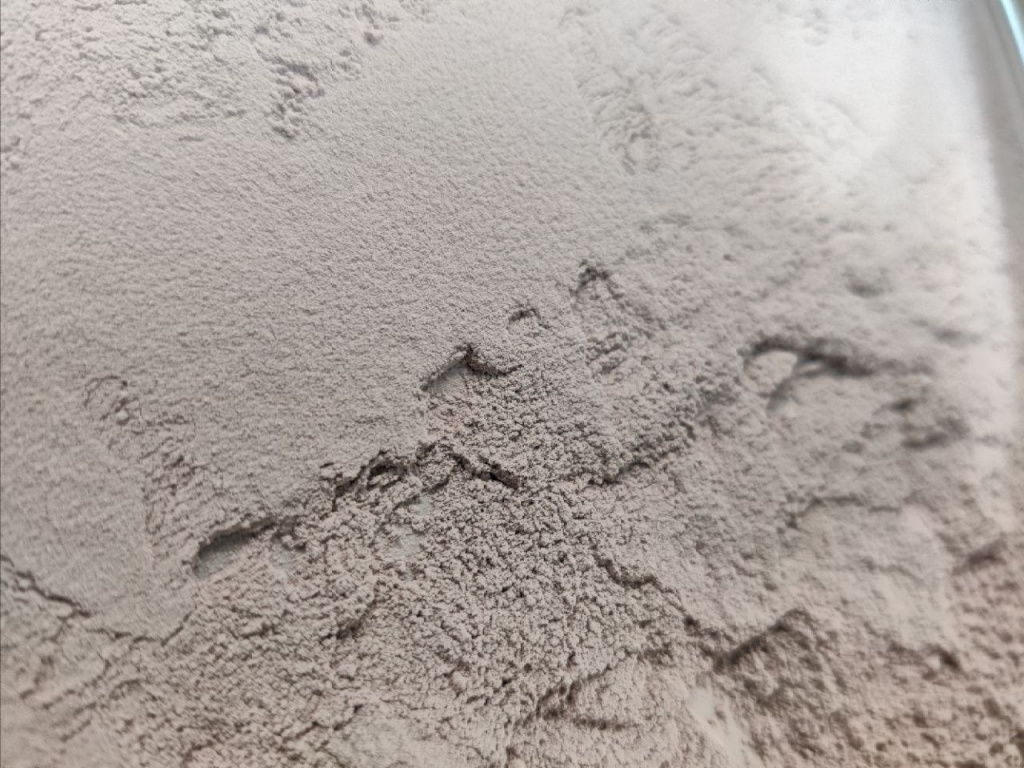
Помимо химического состава исходного порошка присутствуют показатели пористости и вакуумной плотности конечных изделий. Один и тот же оксид алюминия Al2O3 может использоваться и как стержень для заливки металла (требуется высокая пористость материала), и как вакуумный изолятор (материал имеет максимальную плотность). Характеристики внутренней структуры полностью спеченного изделия определяются фракционным составом исходного порошка и параметрами этапов термической обработки. Под каждую задачу подбирается оптимальная порошковая композиция с нужным химическим и гранулометрическим составом.
Область применения технологии
DLP-процесс 3D печати керамическими суспензиями может использоваться в первую очередь для печати конечных изделий: огнеупоров, изоляторов, форсунок, различных элементов ТРД, микропомп, теплообменников, фильтров и других конструкционных деталей, находящихся под тепловыми, электромагнитными, коррозионными и механическими нагрузками.
Также присутствует возможность прямой печати керамических оболочковых форм. Для изготовления стержней и формообразующих поверхностей используется суспензия на основе диоксида кремния (SiO2) или оксида алюминия (Al2O3). Для упрощения процесса удаления стержней после заливки используется специальная модификация суспензии, которая позволяет получать пористую внутреннюю структуру. Шероховатость поверхности Ra полностью спеченных стержней составляет от 1 до 10 мкм в зависимости от задач и исходного сырья.
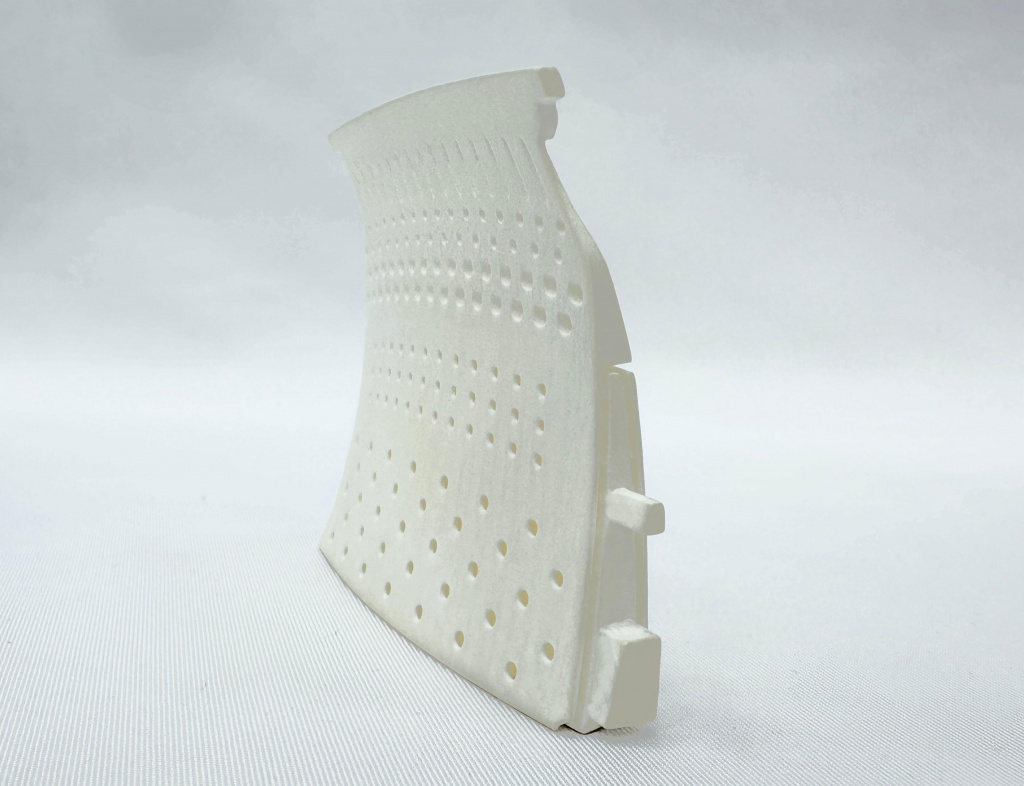